Flange Stress Analysis
- Meena Rezkallah, P.Eng.
- Jun 29, 2017
- 3 min read
The most common design standard for flanges is in ASME Section VIII, Appendix 3—‘‘Mandatory Rules for Bolted Flange Connections.’’ This standard applies in the design of flanges subject to hydrostatic end loads and to establish gasket seating. The maximum allowable stress values for bolting outlined in the ASME code are design values to be used in determining the minimum amount of bolting required under the code. A distinction is made in the code between the design value and the bolt stress that may actually exist in the field. The ASME code Appendix S further acknowledges that an initial bolt stress higher than design value may (and, in some cases, must) be developed in the tightening operation. This practice to increase bolt stress higher than the design values is permitted by the code, provided that regard is given to ensure against excessive bolt loads, flange distortion, and gross crushing of the gasket.
General Requirements
Bolt Loads. In the design of the bolted flange connection, the bolt loads are calculated based on two design conditions of operating and gasket seating.
Operating Condition. The operating condition determines the minimum load according to

where b, G and Pt are defined previously and m is gasket factor expressed as a multiple of internal pressure. The equation is the sum of the hydrostatic end force plus a residual gasket load equaling a multiple of internal pressure.
Gasket Seating. The second design condition requires a minimum bolt load determined to seat the gasket regardless of internal pressure according to

where y is the minimum seating stress for the gasket selected.
PVRC Method. As discussed earlier the PVRC method can be used as an alternate to Wm1 or Wm2 in calculating the bolt loads used in the design of the flange.
Total Required Bolt Areas. These design values on bolt loads are used to establish minimum total cross-sectional areas of the bolts Am. Am is determined as follows:
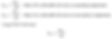
Am is greater of Am1 or Am2 or Amo. Bolts are then selected so that the actual bolt area, Ab, is equal to or greater than Am.
Example Calculation. Using the same application outlined in the ‘‘Gasket Selection’’ section, the following shows the calculation of bolt loads using m and y factors.
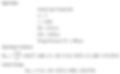
Wm1 > Wm2, therefore Wm1 would govern in the flange design. Note that using the PVRC method, the design bolt load was 645,345 lb, higher than both Wm1 and Wm2. This will be a common occurrence, revealing that higher bolt loads than assumed using m and y factors are required to achieve required leak tightness.
Flange Design. The bolt loads used in the flange design by the code is

Alternately, where additional safety is desired, the code recommends that the bolt load for flange design is actual bolt area (Ab) times the allowable bolt stress (Sa). For critical flanges, it is suggested that a more conservative approach to flange design be adopted, calculating the design bolt load as actual bolt area (Ab) times expected field bolt stress (Se). The expected field-bolt stress (Se) achieved is often
1.5 × Sa. By using this approach a higher bolt load is determined. This will increase the flange thickness. The benefits to increased flange thickness are
Thicker flanges will rotate less and distribute the applied bolt load more uniformly to the gasket.
Thicker flanges require longer bolts. Longer bolts have more strain energy and are more forgiving to joint relaxation.
Finite Element Analysis
Finite Element Analysis (FEA) is being used more frequently to review designs of critical flanges. FEA costs are dropping dramatically while the procedure’s effectiveness to model complex structure is increasing.
FEA can be used to predict the behavior of the flange structure subjected to its operating conditions. It is possible to predict the behavior of the flange structure mathematically because the behavior of the materials can be described mathematically. Hooke’s law describes the mechanical behavior of the metal materials and their elastic response. Other types of stress-strain relationships have been developed to model the nonlinear, plastic behavior of the gasket.
The key is to determine the actual operating stress on the gasket to predict its leak-tightness performance subjected to thermal effects, pressure, bolt stress, relaxation, and flange rotation. #Little_PEng