1.2.1 Fatigue Basics
- Meena Rezkallah, P.Eng.
- Mar 21, 2020
- 2 min read
Updated: Dec 19, 2020
Steels and other metals are made up of organized patterns of molecules, known as crystal structures. However, these patterns are not maintained throughout the steel producing an ideal homogenous material, but are found in microscopic isolated island-like areas called a grains.
Inside each grain the pattern of molecules is preserved. From one grain boundary to the next the molecular pattern is the same, but the orientation differs. As a result, grain boundaries are high energy borders. Plastic deformation begins within a grain that is both subject to a high stress and oriented such that the stress causes a slippage between adjacent layers in the same pattern. The incremental slippages (called dislocations) cause local cold-working. On the first application of the stress, dislocations will move through many of the grains that are in the local area of high stress. As the stress is repeated, more dislocations will move through their respective grains. Dislocation movement is impeded by the grain boundaries, so after multiple stress applications, the dislocations tend to accumulate at grain boundaries, and eventually becoming so dense that the grains "lock up", causing a loss of ductility and thus preventing further dislocation movement. Subsequent applications of the stress cause the grain to tear, forming cracks. Repeated stress applications cause the cracks to grow. Unless abated, the cracks propagate with additional stress applications until sufficient cross sectional strength is lost to cause catastrophic failure of the material. Figure 1-16 illustrates this process.

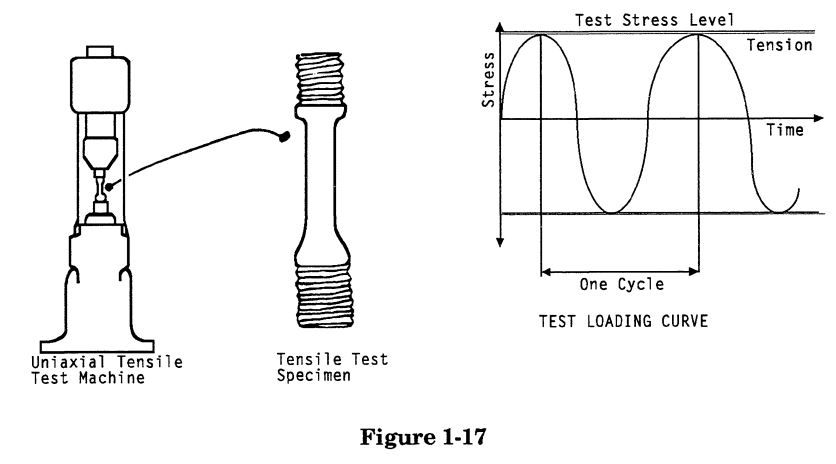
One important consideration is the fact that fatigue cracks usually are initiated at a free surface. Corrosive attack on a material often produces pitting of metal surfaces. The pits act as notches and produce a reduction in fatigue strength. In those specific cases when corrosive attack occurs simultaneously with fatigue loading, a pronounced reduction in fatigue properties results which is greater than that produced by prior corrosion of the surface. When corrosion and fatigue occur simultaneously, the chemical attack greatly accelerates the rate at which fatigue cracks propagate.
Unfortunately, fatigue failures can occur even when the stress in a material is below the yield stress. This is because localized stress concentrations can cause plastic deformation in a relatively few grains despite the fact that the stress over a gross area of the section may be far below the material yield stress. If the section is subjected to a sufficient number of stress cycles, cracks can initiate in highly stressed grains and then propagate throughout the material, ultimately resulting in a fatigue failure of the section as a whole. The fatigue capacity of a material can be estimated through the application of cyclic extensive / compressive displacement loads with a uniaxial test machine, as shown in Figure 1-17.
Sample results for typical ferrous material (with a yield stress of 57,000 psi) are shown below:
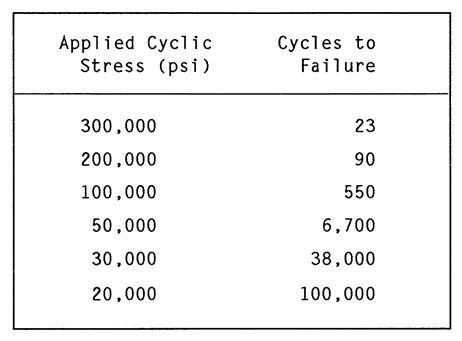
Read More:
To get our piping engineering services, please contact our engineering consultant department for a free quote