1.4 Welding Research Council Bulletin 330
- Meena Rezkallah, P.Eng.
- Apr 3, 2020
- 3 min read
Updated: Dec 20, 2020
The Welding Research Council's Bulletin 330, "Accuracy of Code Stress Intensification Factors for Branch Connections" documented a major attempt to re-assess the existing code requirements for the intensification of stresses at tees and other branch connections. The difficulty of this task was summed up in the bulletin by author E. C. Rodabaugh, who stated:
"We would rate the relative complexity of i-factors for pipe, elbows and branch connections by the ratios 1:5:500. These comments on relative complexity, we think, are relevant at this point because at least some readers will be looking for simple answers to what they perceive to be a simple subject. They will not find any simple answers in this report."
Summarizing the findings of WRC 330 in order of increasing importance:

The following note should be added with regard to branch connection flexibilities: "In piping system analyses, it may be assumed that the flexibility is represented by a rigid joint at the branch-to-run centerlines juncture. However, the Code user should be aware that this assumption can be inaccurate and should consider the use of a more appropriate flexibility representation."
ASME 2/3 and B31.1 users can use the "Branch Connection" expressions for unreinforced fabricated tees whenever r/R <0.5. (Markl's formulas specified that the same stress intensification factor be used on both the branch and header legs of a tee, regardless of relative sizes. The codes noted above permit the reduction of the stress intensification factor at the branch for relative diameters. CAESAR II automatically considers the effects of reduced intersections on the stress intensification factors for these codes unless directed otherwise by the user through the setup file.)
B31.1 erred when including the calculations for branch connection stress intensification factors; instead they should have included the calculations as they appeared in ASME III. (Further clarification of this note is given in note 10 herein.)
B31.3 should include the stress intensification factors for branch connections as per ASME III. (B31.3 uses Markl's original formulas, thus specifying the same stress intensification factor for both the branch and header of a tee, regardless of relative sizes.)
B31.3 should intensify the torsional moment at branch connections, with the torsional intensification factor estimated as: it = (r/R)i0.
B31.3 should eliminate the use of ii = 0.75io + 0.25 for branch connections and tees. It can give the wrong relative magnitude for header moments, and may underestimate the difference between M0 and Mj for r/R ratios between 0.3 and 0.95, and perhaps over-estimates the difference for r/R ratios below 0.2 and for r/R = 1.0.
B31.3 andB31.1 should add restrictions to the stress intensification factor tables indicating that they are valid for R/T < 50.
The codes should add notes that indicate that the stress intensification factors are developed from tests and/or theories based on headers being straight pipe with about two or more diameters length of pipe on either side of the branch.
The codes should also add notes to indicate that for branch connections/tees the stress intensification factors are only applicable where the axis of the branch pipe is within 5 degrees of normal to the surface of the header pipe.
The stress intensification factors for unreinforced fabricated tees, weldolets, and sweepolets should be changed to:
There was not sufficient data available on reinforced fabricated tees for Rodabaugh to make any definitive recommendations regarding them. Rodabaugh does however suggest that the normal usage whereby the width of the pad is taken to be at least equal to the radius of the nozzle should be observed even though not explicitly directed by the code.
12) For t/T ratios of about one or more, stresses tend to be higher in the header, and are fairly independent of the wall thickness of the nozzle. As the t/T ratio gets much smaller than one, the largest stresses shift to the branch. (This finding originally came out of the research for WRC 297.)
Comparisons of WRC 330's proposals for stress intensification factors for various types of tees, versus B31.3 calculated values are shown on the following pages.
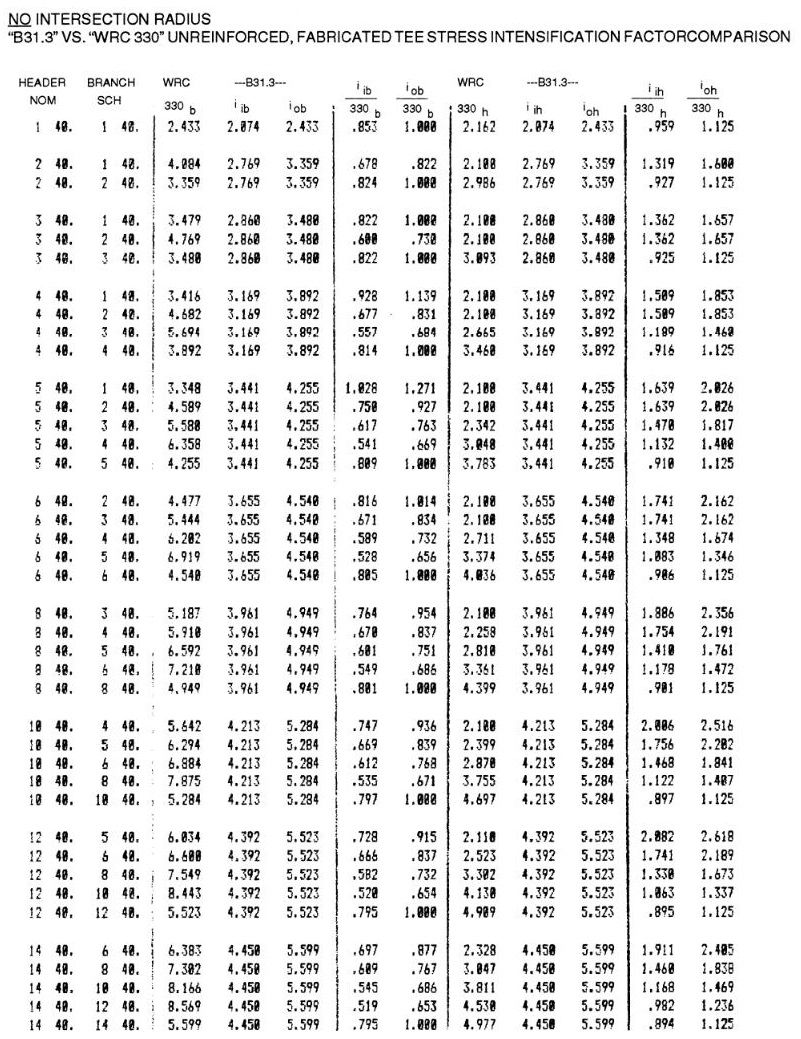
Read More:
To get our piping engineering services, please contact our engineering consultant department for a free quote