4.1.1 Variation of Load Versus Time — Load Types
- Meena Rezkallah, P.Eng.
- Oct 1, 2020
- 8 min read
The force vs. time profiles of the dynamic loads most often encountered during the design of piping are usually one of three types—random, harmonic, and impulse. These profiles, and the load types having them, are described below.
Random: With this type of profile, the load changes direction and/or magnitude unpredictably with time, although there may be predominant characteristics within the load profile. Major types of loads with random time profiles are:
1 - Wind: Wind velocity causes forces as described in Section 2.5.1 Wind Loading notes, that is by the decrease of wind momentum as the air strikes the pipe, creating an "equivalent pressure" on the pipe. Wind loadings, even though they may have predominant directions and average velocities over a given time, are subject to gusting, i.e., sudden changes in direction and velocity. As the observed time period lengthens, the observed number of changes increases in an unpredictable manner as well, eventually encompassing nearly all directions and a wide range of velocities. A typical plot of wind velocity vs. time is shown in Figure 4-1.
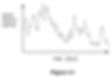
Note that to date, almost all wind design (excluding specialized conditions such as vortex shedding) is done using a static equivalent of a dynamic loading model, increasing the static load by a "gust factor" to account for potential dynamic effects.
2 - Earthquake: Seismic (earthquake) loadings, are caused by the introduction of random motion (accelerations, velocities, and displacements) of the ground, and corresponding inertial loads (the mass of the structure times the acceleration), into a structure through the structure-to-ground anchorage. The random ground motion is actually the sum of an infinite number of individual harmonic (cyclic) ground motions. Two earthquakes may be similar in terms of predominant direction (along a fault, for example), predominant harmonic frequencies (if certain of the underlying cyclic motions tend to dominate), and maximum ground motion, but their exact behavior at any given time may be quite different and unpredictable. A typical plot of earthquake ground acceleration vs. time is shown in Figure 4-2.

Note in many cases, for simplification's sake, seismic design is done using a static equivalent of a dynamic loading model, as described in Section 2.5.2 Earthquake load, however dynamic simulations of seismic loads are usually more accurate. Dynamic analysis of earthquake loads is discussed in detail in in other articles.
Harmonic: With this type of profile, the load changes direction and/or magnitude following to a sine profile, ranging from its minimum to its maximum according to a fixed time period. For example, the load may be described by a function of the form:
F(t) = A + B sin(Ct + D)
Where:
F(t) = force magnitude as a function of time, lb A = mean force, lb B = variation of maximum and minimum force from mean, lb C = angular frequency, radians/sec D = phase angle, radians
Major types of loads with harmonic time profiles are:
1 - Equipment vibration: If rotating equipment attached to a pipe is slightly out of tolerance (drive shaft out of round, for example), it may impose a small cyclic displacement onto the pipe at the point of attachment, where the displacement cycle would most likely correspond to the equipment's operating cycle. The displacement at the pipe connection may be so small as to not even be noticeable, but dynamically it could cause significant problems. The loading vs. time, which can be easily predicted once the equipment's operating cycle and variation from tolerance are known, is shown in Figure 4-3.

2 - Acoustic vibration: If fluid flow characteristics are changed within a pipe (for example if flow conditions change from laminar to turbulent when the fluid goes through an orifice), slight lateral vibrations may be set up within the pipe. Often these vibrations fit harmonic patterns, with predominant frequencies somewhat predictable based upon the flow conditions. For example, Strouhal's equation predicts that the developed frequency (in cycles/sec, or Hz) of vibration caused by flow through an orifice will be somewhere between 0.2 V/D and 0.3 V/D, where V is the fluid velocity (ft/sec) and D is the diameter of the orifice (ft). Wind flow around a pipe sets up lateral displacements as well (a phenomenon known as vortex shedding), with an exciting frequency in the area of 0.18 V/D, where V is the wind velocity and D is the outer diameter of the pipe.
3 - Pulsation: During the operation of a reciprocating pump or a compressor, the fluid is compressed by pistons driven by a rotating shaft. This causes a cyclic change (vs. time) in the fluid pressure at any specified location in the system. If the fluid pressures at opposing elbow pairs or closures is unequal, this creates an unbalanced pressure load in the system. Since the pressure balance changes with the cycle of the compressor, the unbalanced force changes as well. (Note that the frequency of the force cycle will most likely be some multiple of that of the equipment operating cycle, since multiple pistons will cause a corresponding number of force variations during each shaft rotation.) The pressure variations will continue to move along with the fluid, so in a steady state flow condition, unbalanced forces may be present simultaneously at all elbow pairs in the system. The load magnitudes may vary, and the load cycles may or may not be in phase with each other, depending upon the fluid velocity, the distance of each elbow pair from the compressor, and the length of the piping legs between the elbow pairs. A typical loading vs. time profile for pulsation is shown in Figure 4-4.

Impulse: With this type of profile, the load magnitude ramps up from zero to some value, remains relatively constant for a time, and then ramps down to zero again. For rapid ramping times, this type of profile resembles a rectangle. Major types of loads with impulse time profiles are:
1 - Relief valve: When system pressure reaches a dangerous level, relief valves are set to open in order to vent fluid and reduce the internal pressure. Venting through the valve causes a jet force to act on the piping system; this force ramps up to its full value, from zero, over the opening time of the valve. The relief valve remains open (and the jet force remains relatively constant) until sufficient fluid is vented to relief the overpressure situation. The valve then closes, ramping down the jet force over the closing time of the valve. A typical force-time profile for a relief valve load is shown in Figure 4-5.
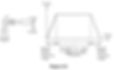
In some cases, analysis of relief valve loads is done using a static equivalent of a dynamic loading model, as described in Section 2.5.3 Quickly Applied Loads [ Fluid Hammer, Relief valves ], however dynamic analyses are usually more accurate.
2 - Fluid hammer: When the flow of fluid through a system is suddenly halted at one point, through valve closure or a pump trip, the fluid in the remainder of the system cannot be stopped instantaneously as well. As fluid continues to flow into the area of stoppage (upstream of the valve or pump), the fluid compresses, causing a high pressure situation at that point. Likewise, on the other side of the restriction, the fluid moves away from the stoppage point, creating a low pressure (vacuum) situation at that location. Fluid at the next elbow or closure along the pipeline is still at the original operating pressure, resulting in an unbalanced pressure force acting on the valve seat or the elbow. The fluid continues to flow, compressing (or decompressing) fluid further away from the point of flow stoppage, thus causing the leading edge of the pressure pulse to move through the line. As the pulse moves past the first elbow, the pressure is now equalized at each end of the pipe run, leading to a balanced (i.e., zero) pressure load on the first pipe leg. However the unbalanced pressure, by passing the elbow, has now shifted to the second leg. The unbalanced pressure load will continue to rise and fall in sequential legs as the pressure pulse travels back to the source (or forward to the sink). A typical force-time profile for a fluid hammer load in a single leg is shown in Figure 4-6. The ramp up time (and corresponding profile) roughly coincides with the elapsed time from full flow to low flow, such as the closing time of the valve or trip time of the pump. Since the leading edge of the pressure pulse is not expected to change as the pulse travels through the system, the ramp down time is the same. The duration of the load from initiation through the beginning of the down ramp is equal to the time required for the pressure pulse to travel the length of the pipe leg.

Analyses of fluid hammer loadings are often done using a static equivalent of a dynamic loading model, as described in Section 2.5.3 Quickly Applied Loads [ Fluid Hammer, Relief valves ], however these types of analysis can be extremely inaccurate.
3 - Slug flow: Most piping systems are designed to handle single-phase fluids (i.e., those which are uniformly liquid or gas). Under certain circumstances, however the fluid may have multiple phases. For example, slurry systems transport solid materials in liquids, and gases may condense, creating pockets of liquid in otherwise gaseous media. Systems carrying multi-phase fluids are susceptible to slug flow.

In general, when fluid changes direction in a piping system, it is balanced by the net force on the elbow. This force, shown in Figure 4-7, is equal to the change in momentum with respect to time, or:

Normally this force is constant, and is small enough that it can be easily absorbed through tension in the pipe wall, to be passed on to adjacent elbows which may have equal and opposite loads, therefore zeroing the net load on the system. Therefore these type of momentum loads are usually ignored by the stress analyst. However, if the fluid velocity or density changes with time, this momentum load will change with time as well, leading to a dynamic (changing) load, which may not be cancelled by the load at other elbows.
For example, consider a slug of liquid in a gas system. The steady state momentum load is insignificant, since the fluid density of a gas is effectively zero. Suddenly the liquid slug hits the elbow, increasing the momentum load by a factor of thousands. This load lasts only as long as it takes for the slug to traverse the elbow, and then suddenly drops to near zero again. A typical profile is shown in Figure 4-8. The exact profile of the slug load depends upon the shape of the slug — the force can be calculated at any given time from

where the A used is the cross-sectional area of the slug instantaneously impacting the elbow. The time duration of the load depends upon the length of the slug divided by the velocity of the fluid.
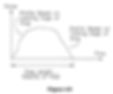
Analysis of slug flow is usually very difficult because the exact shape and length of the slug is rarely known (and rarely constant).
Located in Calgary Alberta, We offer our Piping Engineering Services, Skid Design Services, Pipeline Engineering Services and Structural Engineering Services across Canada. To get our Piping Stress Analysis Services, please contact our Engineering company.
Our professional piping stress engineers have a bachelor's and Masters degree in mechanical / structural engineering and province license (P.Eng.) in Alberta, Saskatchewan, British Columbia and Ontario. We review, validate, certify and stamp piping and structural packages. Also check Industries We Serve.