Bolted Joints
- Meena Rezkallah, P.Eng.
- May 20, 2017
- 6 min read
Bolted Joints
The use of bolted joints is advantageous in the following circumstances:
The components cannot be serviced in line.
The components being joined are not capable of being welded.
Quick field assembly is required.
The component or pipe section must be frequently removed for service.
Bolted piping components are manufactured in accordance with several national standards. Also, several manufacturers produce proprietary bolted connections which offer cost and time savings over conventional flanged connections. However, proprietary designs must be used within the limitations of the applicable codes.
Ductile and Cast-Iron Flanges. Cast-iron flanges are produced in accordance with ASME B16.1. The standard establishes dimensional requirements, pressure ratings, materials, and bolting requirements. The pressure-temperature ratings and materials requirements for cast-iron flanges are the same as those for cast-iron flanged fittings. The pressure-temperature ratings are given in Table A2.6.
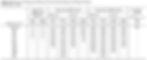
The dimensions for Class 125 and Class 250 cast-iron flanges are listed in Table A2.17. XDimensions for bolting are listed in Table A2.18. Note that the Class 125 and Class 250 flanges can be mated with ASME B16.5 Class 150 and Class 300 steel flanges, respectively. When a Class 150 flange is bolted to a Class 125 cast-iron flange (a flat-faced flange), the steel flange should be flat-faced.


Ductile iron flanges and flanged fittings are manufactured in conformance with the following standards:
ASME B16.42 Ductile Iron Pipe Flanges and Flanged Fittings—Class 150 and 300.
ANSI/AWWA C110/A21.10, C115/A21.15 and C153/A21.53, are listed earlier under ductile and cast iron fittings.
Steel and Nickel-Alloy Flanges. Steel and nickel-alloy flanges up to NPS 24 are produced in accordance with ASME B16.5. Steel flanges NPS 26 (DN 650) through NPS 60 (DN 1500) are produced in accordance with ASME B16.47. Also, orifice flanges are produced in accordance with ASME B16.36. The standards specify materials, dimensions, pressure-temperature ratings, and recommendations for bolting and gasketing. Flanges manufactured to ASME B16.5 and B16.47 may be cast or forged. Also, blind flanges may be fabricated from specific plate materials. The most commonly used materials are forged carbon steel (ASTM A105) and forged low-alloy and stainless steel (ASTM A182). The standards cover seven pressure classes (Classes 150, 300, 400, 600, 900, 1500, and 2500) in a variety of styles and materials. Figures A2.16 and A2.17 show typical flange styles. The dimensions of each style within each pressure class are held constant irrespective of the material. Therefore, within each pressure class, the pressure-temperature rating varies with the material properties (see Figs. A2.1, A2.2, and A2.3).
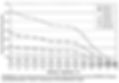

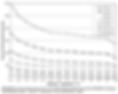
Proprietary Bolted Connections. There are various proprietary bolted pipe joining systems produced that are not formally addressed by any standard. Under the various piping codes, pressure-retaining components not covered by standards specifically cited as acceptable for use under the ‘‘Code’’ may be used provided their design is proved by analysis or proof testing or a combination of both.
Flanges differ in method of attachment to the pipe, i.e., whether they are screwed, welded, or lapped. Contact surface facings may be plain, serrated, grooved for ring joints, seal-welded, or ground and lapped for metal-to-metal contact. Some common types of joints and facings are shown in Fig. A2.18. In Section VIII, Unfired Pressure Vessels, of the ASME Boiler and Pressure Vessel Code, three types of circular flanges are defined, and these are designated as loose-type (Fig. A2.17), integral-type (Fig. A2.16), and optional-type flanges. Under the code, the welds and other details of construction shall satisfy the dimensional requirements stated therein.



Loose-Type Flanges. This (slip-on) type covers those designs in which the flange has no direct connection to the nozzle neck or the vessel or pipe wall and those designs where the method of attachment is not considered to give the mechanical strength equivalent of integral attachment.
Integral-Type Flanges. This type covers designs in which the flange is cast or forged integrally with the nozzle neck or the vessel or pipe wall, butt-welded thereto, or attached by other forms of arc or gas welding of such a nature that the flange and nozzle neck or vessel or pipe wall is considered to be the equivalent of an integral structure. In welded construction, the nozzle neck or the vessel or pipe wall is considered to act as a hub.
Optional-Type Flanges. This type covers designs where the attachment of the flange to the nozzle neck or the vessel or pipe wall is such that the assembly is considered to act as a unit, which shall be calculated as an integral flange, except that for simplicity the designer may calculate the construction as a loose-type flange, provided that stipulated load values are not exceeded.
It is important in flange design to select materials and to proportion dimensions of bolts, flanges, and gaskets to ensure that the necessary compression will be maintained on the joint faces over the expected life of the equipment.
Several distinct phases of the problem are involved: (1) type of flange facing, (2) finish of contact surfaces, (3) gasket type and proportions, (4) bolt load required to secure and maintain a tight joint, and (5) proportions of flange needed to support the bolt load.
Types of Flange Facing.
There are numerous types of contact facings for flanges, the simplest of which is the plain face provided with a ‘‘smooth tool finish.’’ Class 125 cast-iron flanged fittings are provided with this type of facing. For steel flanges and fittings, the typical facings (Fig. A2.19) are taken from the American Standard for Steel Pipe Flanges and Flanged Fittings, ASME B16.5 and ASME B16.47. The raised face, the lapped, and the large male-and-female facings have the same dimensions, which provide a relatively large contact area. Where metal gaskets are used with these facings, the gasket area should be reduced to increase the gasket compression.
The flange-facing types illustrated in Fig. A2.19 range in size and contact area in the following order: large tongue-and-groove, small tongue-and-groove, small male-and-female, and ring joint. Because of the small gasket contact area, a tight joint may be secured with the ring-type facing using low bolting loads, thereby resulting in lowered flange stresses (ASME B16.5). The Sargol and Sarlun facings, which have lips for seal welding, are used frequently for severe service conditions. Seal welding is not always performed since, if it is properly made, a tight joint often can be maintained without the welded seal, thus facilitating disassembly. Typical facing dimensions for Sarlun and Sargol joints are shown in Fig. A2.20. Special types of facing of individual design intended for a specific service are numerous. Economic considerations generally make it desirable to use a standard facing wherever possible.
Selection of the type of facing depends to a considerable extent on the nature of the service. However, it is not possible to determine exactly which facing should be used. Prior experience is usually relied on as a guide. Plain-face joints with red rubber gaskets have been found satisfactory for temperatures up to 220°F (105°C), whereas serrated raised-face joints with graphite-steel-composition gaskets are commonly used for temperatures up to 750°F (400°C). For high temperatures and pressures, faces giving a high contact pressure for a given bolt load are customary, such as the tongue-and-groove and ring joints. However, with high contact pressures, the gasket load must be checked to ensure that the gasket is not over compressed.
An equally successful joint for most types of service can be made by using a profile- serrated metal gasket contacting the flange facing, which may be the plain male- to-male raised-face type.
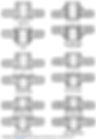

Contact Surface Finish. The surface finish is an important factor in determining the extent to which a gasket must flow to secure an impervious seal. Bolting that results in adequate gasket flow to form a satisfactory seal with a smooth contact surface may be inadequate to secure a tight joint with a rough surface. The finish may vary from that produced by rough casting surfaces to that produced by grinding and lapping. Less gasket flow will be necessary for the latter than for the former. The finish most frequently provided on cast-iron and steel pipe flanges is the smooth tool finish. A serrated finish frequently is provided for steel flanges, particularly when using a graphite-composition gasket with a wide contact area such as is furnished on raised, lapped, or large tongue-and-groove facings. The serrated finish consists of spiral or concentric grooves, usually about 1/64 in (0.4 mm) deep with 12.5 serrations per cm (32 serrations per inch). Where metal gaskets are used, a smooth surface produced by grinding or lapping is usually provided. The Sargol and Sarlun facings mate metal to metal without a gasket, in which case a mirrorlike finish is necessary. This is usually produced by grinding and lapping. It is evident that the surface finish varies with the type of contact face and gasket used and, therefore, should be specified accordingly. #Little_PEng