Joining Ductile or Cast Iron Pipe
- Meena Rezkallah, P.Eng.
- May 27, 2017
- 6 min read

Bell-and-Spigot Joint
This joint for underground cast-iron pipe was developed as long ago as 1785. Standard dimensions are shown in Table A2.22.
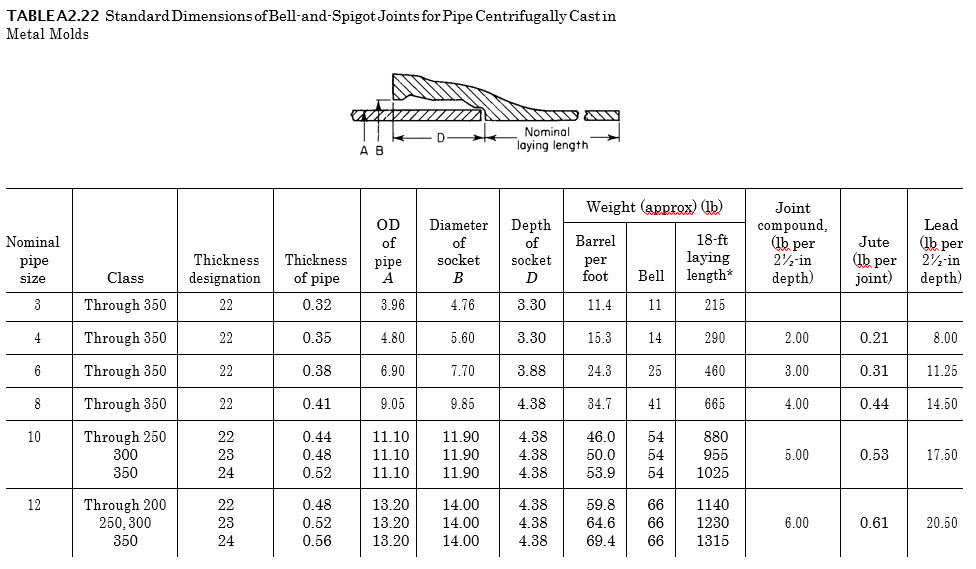
The joint may be made up with lead and oakum, sulfur compounds, or cement. Lead and oakum constitute the prevailing joint sealer for sanitary systems. Bell- and-spigot joints are usually reserved for sanitary sewer systems. These joints are not used in ductile iron pipe.
Mechanical (Gland-Type) Joint
This modification of the bell-and-spigot joints, as designated in Federal Specification WW-P-421 and ANSI/AWWA C111/A21.11, is illustrated in Table A2.23.

This joint is commonly used for low and intermediate-pressure gas distribution systems, particularly those conveying natural gas or dry manufactured gas. Mechanical joints are also used for water lines, sewage, and process piping. In the mechanical (gland-type) joint shown in Fig. A2.30,

the lead and oakum of the conventional bell-and-spigot joint are supplanted by a stuffing box in which a rubber or composition packing ring, with or without a metal or canvas tip or canvas backing, is compressed by a ductile cast-iron follower ring drawn up with bolts. In addition to making an inherently tight joint even under considerable pressure, this arrangement has the advantage of permitting relatively large lateral deflections (3¹⁄₂° to 7°), as well as longitudinal expansion or con- traction. For more details, refer to AWWA C600, Standard for Installation of Ductile-Iron Water Mains and Their Appurtenances.
Tyton Joint
The Tyton joint is designed to contain an elongated grooved gasket. The inside contour of the socket bell provides a seat for the circular rubber in a modified bulb- shaped gasket. An internal ridge in the socket fits into the groove of the gasket. A slight taper on the plain end of the pipe facilitates assembly.
Standard dimensions are given in Table A2.24. The maximum joint deflection angle is 5° for sizes through NPS 12 (DN 300), 4° for NPS 14 (DN 350) and NPS
16 (DN 400), and 3° for NPS 18 (DN 450), NPS 20 (DN 500), and NPS 24 (DN 600). Either all-bell U.S. standardized mechanical joint fittings or bell-and-spigot all-bell fittings with poured or cement joints can be used with Tyton joint pipe.
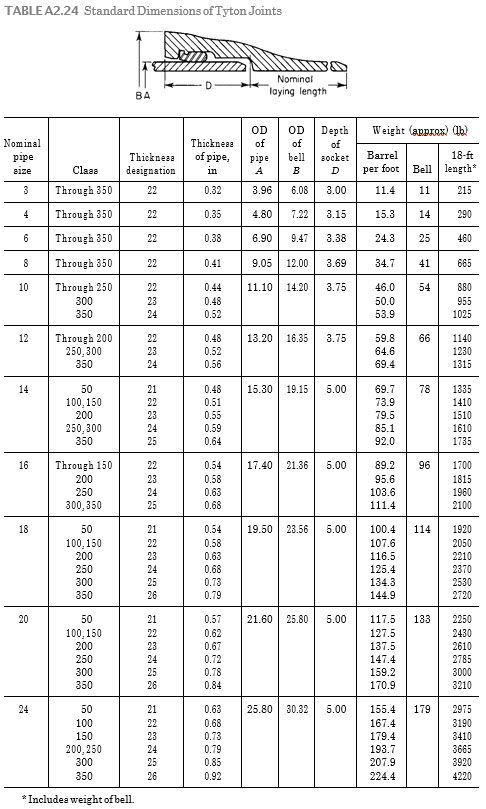
Mechanical Lock-Type Joint
For installations where the joints may tend to come apart owing to sag or lateral thrust in the pipeline, a mechanical joint having a self-locking feature is used to resist end pull. This joint is similar to the gland-type mechanical joint except that in the locked joint the spigot end of the pipe is grooved or has a recess to grip the gasket. Although only slight expansion or contraction can be accommodated in this type of joint, it does allow the usual 3¹⁄₂° to 7° angular deflection. The lock-type joint finds application above ground in the process industries and in river crossings on bridges or trestles, as well as in submarine crossings or in unusually loose or known marshy soils. Where the locking feature is on the spigot rather than on the bell, this type of pipe can be used with the regular line of mechanical joint fittings.
Mechanical Push-On-Type Joint
Where a low-cost mechanical joint is desired, the roll-on type can be used. In this joint, a round rubber gasket is placed over the spigot end and is pulled into the bell by mechanical means, thus pulling the ring into place in the bottom of the bell. Outside the rubber gasket, braided jute is wedged behind a projecting ridge in the bell. This serves to confine the gasket under pressure in the joint. A bituminous compound is used to seal the mouth of the bell and to aid in retaining the hemp and the rubber gasket. Either bell-and-spigot or mechanical (gland-type) fittings are used with this line of pipe. Push-on joints are made in accordance with ANSI/ AWWA C111/A21.11.
Mechanical Screw-Gland-Type Joint
This type of mechanical joint for cast-iron pipe makes use of a coarse-threaded screw gland drawn up by means of a spanner wrench to compress a standard rubber or composition packing gasket. The joint allows from 2° to 7° angular deflection, as well as expansion or contraction without danger of leaks. A lead ring, inserted in the bell ahead of the gasket, seals off the contents of the line from the gasket. The ring also provides an electric circuit through the joint for thawing out frozen underground mains and service lines by the electrical method. The screw-gland joint is used in piping which conveys water, gas, oil, and other fluids at considerable pressure. The gaskets and lead rings are interchangeable with those used in equivalent lines of mechanical joints of the bolted-gland type. A full line of fittings is available for use with screw-gland pipe.
Ball-and-Socket Joints
For river crossings, submarine lines, or other places where great flexibility is necessary, ductile cast-iron pipe can be obtained with ball-and-socket joints of the mechanical-gland types, as shown in Fig. A2.31.

Provision is made for longitudinal expansion and contraction, and a positive stop against disengagement of the joint is a feature of the design. As much as 15° angular deflection can be accommodated without leakage. This pipe is heavy enough to remain underwater where laid without requiring river clamps or anchorage devices. The pipe may be pulled across streams with a cable, since the joints are positively locked against separating, or it may be laid directly from a barge, bridge, or pontoons, without the services of a diver. The mechanical ball-and-socket joint is suitable for use with water, sewage, air, gas, oil, and other fluids at considerable pressure. Either bell-and-spigot or mechanical (gland-type) fittings can be used with this line of pipe, although the integral ball present on the spigot end of some designs has to be cut off before the pipe can be inserted in a regular bell.
Universal Pipe Joints
This type of cast-iron pipe joint (shown in Fig. A2.32)

has a machined taper seat which obviates the need for caulking or for a compression gasket. The joint is pulled up snugly with two bolts, after which the nuts are backed off slightly, thus enabling the lock washers to give enough to avoid over stressing the socket or lugs. Pipe is made in 12- to 20-ft (3.5 to 6-m) lengths to the usual pressure classes and can be bought as Type III under Federal Specification WW-P-421. Universal-joint fittings are available for use with the pipe. This type of joint is used to some extent in pipe diameters of NPS 4 (DN 100) to NPS 24 (DN 600) for underground water supply systems; but it is not considered suitable for gas service, and it does not permit much angular displacement or expansive movement.
Compression-Sleeve Coupling
The type of joint shown in Fig. A2.33 is used with plain-end pipe of either cast iron or steel. It is widely known under the trade names of Dresser coupling and Dayton coupling. Compression sleeve couplings are used extensively for air, gas, oil, water, and other services above- or underground. With a joint of this type, it is necessary to anchor or brace solidly at dead ends or turns to prevent the line from pulling apart. Compression couplings and fittings with screwed packing glands are available for use with small-size cast-iron or steel pipe. In welded transmission lines for oil or gas where any significant change in temperature is expected, a certain percentage of the joints may be made up with compression couplings instead of welding in order to allow for expansion.
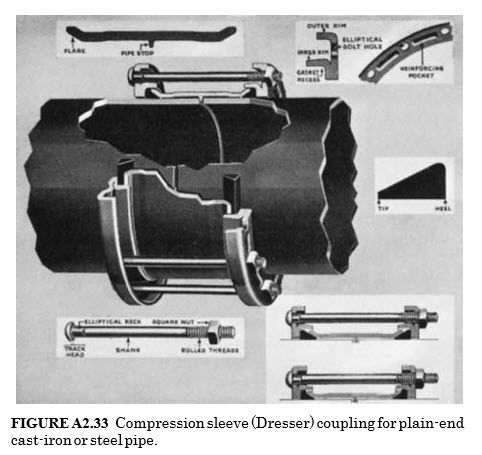
Grooved Segmented-Ring Coupling
The type of split coupling shown in Fig. A2.34 is used with either ductile cast-iron or steel pipe that has grooves near the ends which enable the coupling to grip the pipe, in order to prevent disengagement of the joint. The couplings are manufactured in a minimum of two segments for small pipe sizes and several segments for large pipe sizes. Grooved-end fittings are available for use with the couplings. With proper choice of gasket material, the joint is suitable for use above- or underground with nearly any fluid or gas. The joint’s advantages are its
Ability to absorb minor angular and axial deflections
Ability to increase gasket sealing force with increased system pressure
Refer to AWWA C.606, Standard for Grooved and Shouldered Joints.
Simplicity for rapid erection or dismantling for systems requiring frequent disas- sembly.
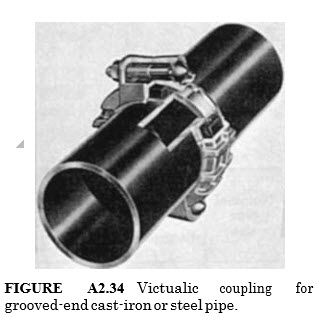
The coupling is also available in a style where grooving of the pipe ends is not required. Joint separation is prevented by the use of hardened steel inserts (teeth) which grab the mating pipe ends.
Flanged Joints
Flanged ductile or cast-iron pipe is used above ground for low and intermediate pressures in water-pumping stations, gas works, power and industrial plants, oil refineries, booster stations for water, and gas and oil transmission lines. Cast iron flanges usually are faced and drilled according to ASME B16.1. For flanged joints in a ductile iron pipe, refer to ASME B16.42, ANSI/AWWA C110/A21.10, C111/ A21.11, C115/A21.15, and C153/A21.53. Cast-iron pipe is made both with integrally cast flanges and with threaded companion flanges for screwing onto the pipe (as shown in Figs. A2.35 and A2.36).
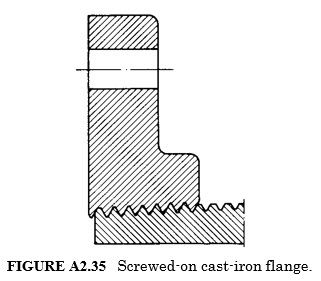

In the latter case, the outside diameter of the pipe conforms to iron pipe size (IPS) dimensions to allow for the threads provided. It is available in sizes NPS 3 (DN 50) through NPS 24 (DN 600) and in length to 18 ft (5.5 m). For lengths less than 3 ft (1 m), in sizes NPS 3 (DN 50) through NPS 12 (DN 300), the flanges may be cast integrally with the pipe, rather than screwed on the pipe, at the manufacturer’s option.
Standard dimensions of flanged joints for silver brazing are shown in Table A2.25.
