Valves Types
- Meena Rezkallah, P.Eng.
- Jul 3, 2017
- 16 min read
Dear engineers, If you are searching for "Valves" or "Valves Types" the article below present all the information about valves types, installation and operation.
Ball Valves
The ball valve (Fig. A10.20) is a quarter-turn valve suitable for clean gas, compressed air, and liquid service. They also can be used for slurry service, but provisions for prevention of crud buildup must be made.

The use of soft-seat materials such as nylon, delrin, synthetic rubbers, and fluorinated polymers imparts excellent sealing ability. With fluorinated polymer seats, ball valves can be used for service tempera-tures ranging from —450 to 500°F (—270° to 260°C); with graphite seats, service temperatures to 1000°F (538°C) or even higher are possible. Also, with metal- backing seats, the valves can be used in fire-safe services. Ball valves are similarto plug valves in operation. They are nonbinding and provide leak-tight closure. The valves exhibit negligible resistance to flow because of their smooth body and port.
Construction of a Ball Valve
Major components of the ball valve are the body, spherical plug, and seats. Ball valves are made in three general patterns: venturi port, full port, and reduced port. The full-port valve has an inside diameter equal to the inside diameter of the pipe. In the venturi and reduced-port styles, the port is generally one pipe size smaller than the line size. Stem sealing is accomplished by bolted packing glands and O-ring seals. Valves are also available with a lubricant-seal system that is similar to that available for plug valves. A typical lubrication system is illustrated in Fig. A10.21.
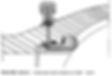
A ball valve may be unidirectional, bidirectional, or multidirectional, depending on the number of valve ports and the number of valve seats. Therefore, ball valves are referred to as 2-way, 3-way, 4-way, or 5-way multiport valves. A 2-way ball valve with a single seat will be unidirectional with the flow direction indicated. Even a 3-way, 4-way, or 5-way ball valve can be unidirectional when flow must enter through a designated port. A 2-way ball valve provided with two seats, one on the upstream side and the other on the downstream side of the ball, is termed a bidirectional valve. Multiple-port ball valves permit flows in more than one direction, thus eliminating the need for several valves.
Ball valves are manufactured in several different body configurations: top entry, side entry, split body, and three-piece body. The valve ends are available as butt welding, socket welding, flanged, threaded, soldering, or brazing ends.
Ball valves are manufactured in high and low-pressure classifications. The advances in ball valve designs have made it possible to use these valves in high pressure and high-temperature applications.
Types of Ball Valves
The following provides a brief description of types of ball valves:

Split-Body Ball Valve. The split body design consists of a two-part body, a cover, ball, seat rings, stem, and other internals. The two-part body is held together by a flange connection. One body part is smaller than the other. The ball is inserted in the larger body part, and the smaller body part is assembled by a bolted connection. The stuffing box is constructed integral with the larger body part. On smaller size split-body ball valves, the two-part body is joined by threaded connection. The flanged or threaded joint between the two-part body is an added source of potential leakage. Flanged end connections are commonly available on all sizes; however, they are standard for large size valves. NPS 2 (DN 50) and smaller split-body ball valves are furnished with screwed ends. The split-body ball valves are manufactured in sizes ranging from NPS ¹⁄₂ (DN 15) through NPS 36 (DN 900). Refer to Fig. A10.22.
Top-Entry Ball Valve. Top-entry ball valves allow access to valve internals for assembly, disassembly, repair, or maintenance by removal of the valve bonnet-cover. The valve is not required to be removed from the pipeline. Refer to Fig. A10.23.
End-Entry Ball Valve. End-entry ball valves have a single-piece body. The ball is inserted from one end and is retained by an insert. These valves have flange or screwed-end connections. This design is commonly used for inexpensive small valves. They are also available in larger sizes up to NPS 6 (DN 150).
Three-Piece—Body Ball Valve. The middle part of the valve is the major part that holds all valve internals, and the stem passes through a hole in the top. Two end caps are held together with the middle body by bolts or studs and nuts. The end connections are part of the end caps, and they may be butt-welding, socket welding, threaded, or flanged. This design is available in sizes ranging from NPS ¹⁄₂ (DN 15) through NPS 36 (DN 900). The two end cap joints are two additional sources of potential leakage. The trunnion-mounted ball-valve design is used with split-body large size valves, whereas the floating-ball design is the most common design for all other types of ball valves. The torque required to actuate a trunnion-mounted ball valve is substantially smaller than the torque required for a floating-ball design.
Lubricated or Nonlubricated Ball Valves. Like other valves, the stem sealing is usually accomplished by bolted packing glands and O-ring seals. Some valve designs are available with a lubricant-seal system similar to the one used in plug valves. Such a design is shown in Fig. A10.21. The valves with lubrication seal systems are termed lubricated ball valves, while others are called nonlubricated.
Advantages of Ball Valves
The following are the advantages of ball valves:
Provides bubble-tight service.
Quick to open and close.
Smaller in size than a gate valve.
Lighter in weight than a gate valve.
Multiport design offers versatility not available with gate or globe valves. It reduces the number of valves required.
Several designs of ball valves offer flexibility of selection.
Can be used in clean and slurry applications.
High-quality ball valves provide reliable service in high-pressure and high-temperature applications.
Force required to actuate the valve is smaller than that required for a gate or a globe valve.
Disadvantages of Ball Valves
They are not suitable for sustained throttling applications.
In slurry or other applications, the suspended particles can settle and become trapped in body cavities causing wear, leakage, or valve failure.
Typical Applications of Ball Valves
The following are some typical applications of ball valves:
Air, gaseous, and liquid applications requiring bubble-tight service
Low-point drains and high-point vents in liquid, gaseous, and other fluid services
Instrument root valves
Cooling water and feedwater systems
Steam service
Plug Valves
Plug valves, also called cocks, generally are used for the same full-flow service as gate valves, where quick shutoff is required. They are used for steam, water, oil, gas, and chemical liquid service. Plug valves are not generally designed for the regulation of flow. Nevertheless, in some applications, specially designed plugs are used for this purpose, particularly for gas-flow throttling.
Plug valves generally can be readily repaired or cleaned without necessitating removal of the body from the piping system. They are available for pressure service
from vacuum to 10000 psi (69000 kPa) and temperatures from —50 to 1500°F (—46 to 816°C). Also, plug valves are available with a wide variety of linings suitable for many chemical service applications.
Construction of a Plug Valve
The basic design of plug valves is illustrated in Fig. A10.24.

Full flow is obtained when the opening in the tapered plug is aligned in the direction of flow. When the plug is rotated a quarter turn, flow is terminated. The body and tapered plug represent the essential features in plug valves. Careful design of the internal contours of the valve produces maximum flow efficiency. The port in the tapered plug is generally rectangular. However, valves are also available with round ports. Major valve patterns or types are identified as regular, venturi, short, round-port, and multiport.
Plugs are usually tapered downward, while in some cases they are tapered upward. Most of the plug valves are top entry. In top-entry plug valves, the tapered plug is installed from the top of the valve. In some cases the plug is tapered upwards and is installed from the bottom opening in the valve body. Such a plug is called bottom entry or inverted plug valve.
Plug valves are also available with cylindrical plugs. The cylindrical plugs provide for larger port openings equal to or greater than the pipe flow area.
The regular pattern employs the tapered form of port openings, the area of which is from 70 to 100 percent of the internal pipe area. In some cases, the face-to-face lengths are greater than those of standard gate valves. The venturi pattern provides streamlined flow and thus permits reduction in the port size. The port opening area is approximately 40 to 50 percent of the internal pipe area. In most of the plug valves, the port opening varies from 60 to 70 percent of the pipe area. The round-port full-bore pattern has a circular port through the plug and body equal to or greater than the inside diameter of the pipe or fitting. Operating efficiency is equal to or greater than that of gate valves of the same size.Use of multiport valves is advantageous in many installations because it provides simplification of piping and convenience in operation. One three-way or four-way multiport valve may be used in place of two, three, or four straightway valves. Refer to Fig. A10.25.

Types of Plug Valves
The following describes salient features of different types of plug valves:
Lubricated Plug Valves. The plug in a lubricated plug valve is provided with a cavity in the middle along its axis. This cavity is closed at the bottom and fitted with a sealant-injection fitting at the top. The sealant is injected into the cavity, and a check valve below the injection fitting prevents the sealant from flowing in the reverse direction. The sealant oozes out from the center cavity through radial holes into lubricant grooves that extend along the length of the seating surface of the plug. The sealant or the lubricant performs the following functions:
Establishes a renewable seal between the plug and the body. As a result, internal leakage is prevented or minimized.
Protects the seating surfaces against corrosion.
Acts as a lubricant, thus reducing the force required to open or close the valve.
The lubricant pressure developed by a turn of the lubricant screw or injection of lubricant with a pressure gun exerts a powerful hydraulic jacking action on the plug, momentarily lifting it from the seat and making it easy to turn. Since the lubricant pressure is greater than the line pressure, it is virtually impossible for solids to lodge between the valve body and plug.
The type of sealant to be used must be compatible with the flow medium in the pipe. The sealant must not dissolve or be washed away by the flow medium. The washed-away or dissolved sealant could contaminate the fluid, and the seal between the plug and the body would be destroyed, resulting in leakage. In addition, the sealant used must be able to withstand the flow-medium temperature.
Lubricated plug valves are normally manufactured in sizes ranging from NPS
¹⁄₂ through 36 (DN 15 through 900). They can be used in applications with pressures over 2500 psi (17250 kPa). They have been used in services involving air, gases, acids, alkalis, water, steam, oils, fuels, among others. Lubricated plug valves are less subject to seizing or wear and may exhibit somewhat greater resistance to corrosion in some service environments.
Nonlubricated Plug Valves. Nonlubricated plug valves contain an elastomeric body liner or a sleeve, which is installed in the body cavity. The tapered and polished plug acts like a wedge and presses the sleeve against the body. Thus, the nonmetallic sleeve reduces the friction between the plug and the body. Nonlubricating plug valves are used where maintenance must be kept to a minimum. Like lubricating plug valves, these valves also provide a bubble-tight closure and are of compact size.
Lubricants
The word lubricant does not precisely define the part this material plays in the efficient functioning of lubricated plug valves. More properly such valves might be called plastic sealed valves, and the lubricant could better be designated plastic sealant. The use of an effective lubricant is important, as, in operation, the valve structure and plastic scaling film are an integral unit, and each component is dependent on the other for ultimate performance. The lubricant in effect becomes a structural part of the valve, as it provides a flexible and renewable seat. This eliminates the necessity of force fits and metal-to-metal distortable-seat contacts to effect a seal. For this purpose, the lubricant must exhibit proper elasticity as well as resistance to solvents and chemicals to avoid the destructive action of the line fluid and to form an impervious seal around each body port, even under pressure. The film of lubricant also protects the metal surfaces between the plug and body from corrosion. The seal formed by the lubricant transmitted in a system of lubricant grooves circuiting each port aids in maintaining the essential film on the metal, closure surfaces.
Advantages of Plug Valves
The following summarizes the advantages of plug valves:
Simple design with few parts.
Quick to open or close.
Can be serviced in place.
Offers minimal resistance to flow.
Provides reliable leaktight service. Seal can be maintained by injection of sealant or by replacement of sleeve, in addition to utilizing the wedging action of a tapered plug.
Multiple port design helps reduce number of valves needed and permits change in flow direction.
Disadvantages of Plug Valves
The disadvantages include:
Requires greater force to actuate, due to high friction.
NPS 4 (DN 100) and larger valves require use of actuators.
Reduced port, due to tapered plug.
Typically, plug valves may cost more than ball valves.
Typical Applications of Plug Valves
As indicated earlier, the plug valves can be and have been used in many different fluid services. They perform well in slurry applications. They are primarily used in bubble-tight services as on-off stop valves. The wiping-off action of a plug does not permit suspended particles to accumulate and form crud. The following are some typical applications of plug valves:
Air, gaseous, and vapor services
Natural gas piping systems
Coal slurries, mineral ores, mud, and sewage applications
Oil piping systems
Vacuum to high-pressure applications
Diaphragm Valves
All diaphragm valves are bidirectional. They can be used as on-off and throttling valves. Diaphragm valves offer advantages in certain low-pressure applications not possible with other types of valves. Their fluid passages are smooth and streamlined, minimizing pressure drop. They are suitable for moderate throttling applications, and they exhibit excellent leak-tight characteristics, even when conveying liquids containing suspended solids. The fluid stream is isolated from the working parts of the valve, preventing contamination of the fluid and corrosion of the operating mechanism. Since there is no leak path around the valve stem, the valve is virtually leak tight. This feature makes the valve indispensable where leakage into or out of the system cannot be tolerated.
The maximum pressure that these valves can be subjected to is a function of the diaphragm material and the service temperature. Also, the rated design life of the valve is influenced by the service conditions. Furthermore, the system hydrostatic test pressure must not exceed the maximum pressure rating of the diaphragm.
Construction of a Diaphragm Valve
Diaphragm valves (Fig. A10.26) consist of a rigid body formed with a weir placed in the flow path, a flexible diaphragm which forms the upper pressure boundary of the valve, a compressor which is used to force the diaphragm against the weir, and the bonnet and hand wheel which secure the diaphragm to the body and actuate the compressor.

Diaphragm valves are manufactured in a variety of end connections: welding- end socket or butt welding; flanged, screwed, or threaded; clamp ends or grooved ends; solvent cement joint ends for themoplastic valves; and male sanitary threaded ends. The valve body is available in two patterns: tee-pattern and angle pattern.Diaphragm valves are available in a wide choice of body, diaphragm, and lining materials that are suitable for service with a wide variety of chemicals. For severe corrosive applications, diaphragm valves are made of stainless steel or PVC plastics, or they are lined with glass, rubber, lead, plastics, titanium, or still other materials. Some of the common materials used for diaphragms are listed in Table A10.10.

Adjustable travel stops are used to prevent excessive compression of the diaphragm. The adjustable travel stop can be enclosed in a temper-proof housing. The temper-proof housing prevents inadvertent mishandling after the travel length is set. It requires a special tool to open the housing and to make an adjustment in the travel length.
When an actuator is required, it should be sized and tested by the valve manufacturer and furnished with the valve as an assembled unit with settings made and verified in the shop.
Types of Diaphragm Valves
Primarily there are two basic designs of diaphragm valves: weir and straight-through types. The body interior and the end flanges can be lined to make the diaphragm valves suitable for corrosive applications. Various lining materials can be used, depending upon the application.
Weir-Type Diaphragm Valves. As shown in Fig. A10.26, a weir is provided as an integral part of the valve body. The weir acts as the valve seat against which the diaphragm is compressed to stop the flow. This type of diaphragm valve is generally produced in large sizes. The raised weir reduces the amount of diaphragm travel from the fully open to the fully closed position, thus reducing the amount of stress and strain in the diaphragm.
Straight-Through Diaphragm Valves. Variations of the weir diaphragm valve are the straightway (Fig. A10.27) and the full-bore types (Fig. A10.28). When the straightway valve is open, its diaphragm lifts high for full streamline flow in either direction. When the valve is closed, the diaphragm seals tight for positive closure even with gritty or fibrous materials in the line. The full-bore type of valve is most extensively used in the beverage industry. It permits ball-brush cleaning with either steam or caustic soda, without opening or removing the valve from the line.
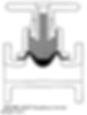

Advantages of Diaphragm Valves
The following summarizes some distinct advantages of diaphragm valves:
Can be used as on-off and throttling service valves.
Offer good chemical resistance due to variety of linings available.
Stem leakage is eliminated.
Provides bubble-tight service.
Does not have pockets to trap solids, slurries, and other impurities. It is suitable for slurries and viscous fluids.
These valves are particularly suitable for hazardous chemicals and radioactive fluids.
These valves do not permit contamination of flow medium, thus they are used extensively in food processing, pharmaceutical, brewing, and other applications which cannot tolerate any contamination.
Disadvantages of Diaphragm Valves
The weir may prevent full drainage of piping.
Working temperatures and pressures are limited by the diaphragm material. Generally the pressures are limited to 200 psi (1380 kPa) and temperatures up to 400°F (204°C).
The diaphragm may also limit the hydrostatic pressure.
The diaphragm may experience erosion when used extensively in severe throttling service containing impurities.
Diaphragm valves are available in limited sizes, usually NPS ¹⁄₂ to 12 (DN 15 to 300).
Typical Applications of Diaphragm Valves
Clean or dirty water and air service applications
Demineralized water systems
Corrosive applications
Radwaste systems in nuclear facilities
Vacuum service
Food processing, pharmaceutical, and brewing systems
Butterfly Valves
Butterfly valves are used to control and regulate or throttle the flow. They are characterized by fast operation and low-pressure drop. They require only a quarter- turn from closed to full-open position. A typical flanged butterfly valve is illustrated in Fig. A10.29.
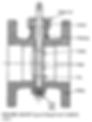
Butterfly valves are produced in sizes ranging from NPS 1¹⁄₂ (DN40) to over NPS 200 (DN 5000). They are usually manufactured in flanged, wafer, and lug, or single-flange-type designs. The welding-end style is a specially engineered valve for a specific application. Threaded-end, grooved-end, and shouldered-end butterfly valves are also available to satisfy the joint type selected for the piping system. Butterfly valves are produced with metal-to-metal seats, soft seats, and with fully lined body and disc. The soft seats permit bubble-tight shutoff and the full lining enhances erosion and corrosion resistance.
Butterfly valves are suitable for low-pressure and low-temperature applications as well as high-pressure and high-temperature applications. The term high-performance butterfly valve is intended to signify their suitability for moderate to high pressure and temperature services.
The butterfly valves have a low-pressure drop and high-pressure recovery factor. They are suitable for low-pressure drop applications. These valves are extensively used in large water transmission, distribution, and cooling water lines.
Construction of a Butterfly Valve
A butterfly valve has a short circular body, a round disc, shaft, metal-to-metal or soft seats, top and bottom shaft bearings, and the stuffing box. The valve body may have flanged ends, lugs, or wafer style (Fig. A10.30) configurations to be installed between pipe flanges. The welding-end (Fig. A10.31) butterfly valves are usually large and have butt-welding ends. Sometimes butterfly valves are manufactured in rectangular or square configurations.


The wafer-style butterfly valves are usually available in sizes NPS 12 (DN 300) or smaller. The limitation on size is essentially imposed by the difficulty of holding the larger weight valve in place between the flanges. The lug and flanged-end butterfly valves are available in all sizes and pose no problem in installation between flanges except for the normal problems associated with warped-flanged surfaces and uneven torquing of bolts.
Types of Butterfly Valves
Low Pressure or Concentric Butterfly Valves. In low pressure and low temperature designs of a butterfly valves, the disc and shaft axes are concentric. In open position, the disc divides the flow in two equal halves, with the disc in the middle and parallel to the flow. These valves are provided with resilient seats. These valves are available as lined or unlined. Most commonly used lining and seating materials include: Buna N, Neoprene, Fluorcel, Hypalon, EPDM, TFE, Viton, among others. The application temperature is limited by the temperature capability of the resilient material. These valves are generally produced in Classes 150 and 300.
High-Performance or Eccentric Butter fly Valves. The disc in high performance butterfly valves is offset from the center of the valve, and the shaft is also offset from the center of the disc. The offsets provided allow the disc to move eccentrically uninterrupted away from or toward the valve seat. Thus, the uninterrupted motion of the disc until it seats against the valve seat prevents unwanted wear and tear of the valve seat and disc due to friction and rubbing of the seating surfaces. The high-performance butterfly valves are used for on-off and throttling services. Some butterfly valve manufacturers produce high performance butterfly valves with triple offset, which enhances their actuation and leak tightness.
Advantages of Butterfly Valves
The following summarizes the advantages of butterfly valves:
The compact design requires considerably less space, compared to gate, globe, or other valves.
Light in weight.
Quick acting; as a quarter-turn valve, it requires less time to open or close.
It is available in large sizes, ranging from NPS 1¹⁄₂ (DN 40) to over NPS 200 (DN 5000).
They have low-pressure drop and high-pressure recovery.
Provide bubble-tight service.
Disadvantages of a Butterfly Valve
Throttling service is limited to low differential pressure.
Throttling is restricted to a 30- to 80-degree disc opening. Location of valve, pipe routing, free, and closed discharge are to be considered while using a butterfly valve in a throttling application.
Cavitation and choked flow are two potential concerns.
The disc movement is unguided and affected by flow turbulence.
Typical Applications of Butterfly Valves
Concentric or low-pressure and low-temperature butterfly valves, the high-performance butterfly valves, cover a wide range of applications. These applications include:
Cooling water, air, gases, and other similar applications, such as fire protection, circulating water, et cetera
Corrosive services requiring lined valves
Food processing, chemical, and pharmaceutical services
Slurry and similar services
High-pressure and high-temperature water and steam services
Throttling service involving low differential pressures, as in cooling water or air supply systems
Vacuum service
Application Considerations for Butterfly Valves
It is noted that the disc of butterfly valve is unguided; therefore, operability of the valve is affected by the flow characteristics. A butterfly valve should not be located just downstream of a source of flow turbulence, such as pump-discharge nozzle, elbow, control valve, or a tee-branch. To minimize the effects of flow turbulence on the valve, attempts should be made to
Locate the valve 4 to 6 diameters downstream of the source of flow turbulence.
Orient the valve shaft in the same plane as the elbow or the pump outlet configuration. When there is more than one component on the upstream side of the valve, then the component adjacent to the valve is to be considered in determining the valve-shaft orientation.
When used in throttling applications, an attempt must be made to provide an adequate straight length of pipe downstream of the valve to allow the flow turbulence to subsidize prior to diverting the flow.
Butterfly valves are essentially bidirectional. In the case of high-performance butterfly valves, and sometimes in the case of low-pressure and low-temperature butterfly valves, the valve design may require more actuating torque to open or close the valve when the flow is reversed. In such cases, the valve manufacturer must be contacted to ensure that the valve is designed and the actuator is sized for flow in both directions.