Environmental Factors affecting Piping Design
- Meena Rezkallah, P.Eng.
- Dec 14, 2017
- 6 min read
The generalized definition of the term stress, when used in a structural connotation, is force per unit area. The mathematical equation that relates the stress to the load F and the load resisting area A is

The loss of a piping system’s pressure or structural integrity is invariably the result of its having attained a higher-than-acceptable state of stress. In the preceding section, it was shown that such an increase in the state of stress of a piping system could result from the application of one or more external (or internal) loads. In terms of Eq. (B2.8), it can be said that loading conditions or loads increase the state of stress of the system by increasing the value of the numerator F of the equation. However, there is a second mechanism through which the state of stress of a piping system may increase, perhaps to the point at which a failure occurs. That mechanism is the loss, or deterioration, of the load-resisting area A.
In this chapter the various mechanisms that result in the loss or deterioration of the viable load-resisting base material of a piping system are titled environmental factors. An attribute that is common to all environmental factors is that they effectively shorten the useful life of the piping system compared to what it would be if the factors were not present. The following discussion is limited to four specific environmental factors: corrosion, erosion, physical damage, and erosion-corrosion.
Corrosion
Within the context of this chapter, corrosion is the loss of load-carrying material in the pipe wall due to an electro-chemical reaction between the piping material and the process fluid, or the environment. Corrosion is normally accounted for in design by the provision of additional material in the pipe wall, the use of a suitable coating or lining, or the specification of a corrosion-resistant material. Frequently, the method used to deal with corrosion depends upon the corrosion rate. For steel corroding in water, the corrosion rate is strongly influenced by the amount of oxygen present and by the temperature. The effect of these variations
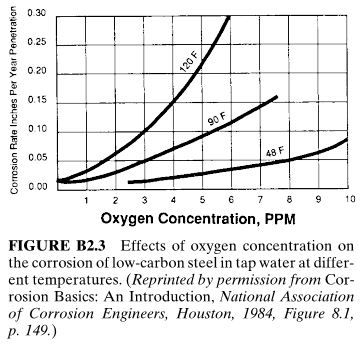
is shown in Fig. B2.3. Similar data exist in the literature for a wide variety of piping system materials and corrodants. Through the use of these data, the corrosion rate for a given process can often be estimated.
When corrosion is anticipated to occur at a slow, regular rate and this rate can be reliably predicted, it may be accommodated by the provision of excess material in the pipe wall known as the corrosion allowance. This excess material will be consumed over the design life of the piping system and therefore cannot be counted upon to serve any other purpose such as pressure integrity, structural strength, or mechanical strength. The relationship of the corrosion allowance to the other components of the total pipe wall thickness was discussed earlier in the section ‘‘Design Pressure.’’
In cases in which the corrosion rate is prohibitively high or would result in unacceptable contamination of the process fluid, a pipe lining or corrosion-resistant piping material may be specified. Linings tend to be fragile; therefore, their use is limited to applications in which abrasion or other physical injury is not likely to occur. Many linings are temperature-sensitive and cannot be used in extreme-temperature service. Most lined pipe is fabricated from plain-carbon steel, although fiberglass-reinforced plastic pipe with an integral, chemically resistant plastic lining is available. Joining methods are a significant factor in lined pipe design, and the joints must not allow any corrosion-sensitive material to be exposed to the process stream. Abrasion or other physical attack may damage a lining and expose the corrosion-sensitive substrate. In such cases, a homogeneous material is frequently warranted. If the original corrosion-resistant surface is physically damaged, the remaining material will continue to resist corrosion. Many corrosion-resistant materials have good high-temperature strength properties and as such are used where linings or plain-carbon steels will not survive. Many near-ambient-temperature, high-corrosion-rate applications can be successfully and economically accommodated by the use of plastic pipe.
Erosion
Erosion is the wearing away of a surface by abrasion. The abrasion may be the result of particles suspended in the fluid stream, or it may be the result of direct action by the fluid itself. When the erosion rate is small and consistent, and reliable quantitative data concerning that erosion rate are available, an erosion allowance may be provided in the design. The erosion allowance is analogous to the corrosion allowance discussed earlier in the sections ‘‘Design Pressure’’ and ‘‘Corrosion.’’ Excess material, over and above that required for pressure integrity and structural and mechanical strength, is provided. This excess material is allowed to waste away over the design life of the piping system. When the erosion process is not readily quantified, a more qualitative approach to design is normally taken. One approach is to specify special erosion-resistant piping system materials. High-hardness materials are generally effective in resisting erosion. An alternative approach is to modify the piping system geometry to minimize or eliminate turbulent flow, direct pipe wall impingement, and vortex flow,all of which increase piping system erosion.
Physical Damage
Physical damage or abuse also can be a significant factor in the design of piping systems. This is particularly true of low-pressure, thin-walled piping, which has little resistance to external loadings. Direct buried pipe is subject to damage from soil pressure and loads from overhead traffic. Uniformly distributed soil pressure loads can normally be estimated with reasonable accuracy and the pipe designed for these loads using methods described in the literature. The effects of heavy concentrated overhead loads cannot be accounted for as easily. Consequently, pipelines which run under heavily trafficked roads or railroad tracks are frequently run through oversized sleeves or conduits which prevent the imposed loads from being directly transmitted to the pipe.
Piping systems of all sizes that carry important services, toxic fluids, or high-pressure, high-temperature fluids should be physically protected from impact from passing motor vehicle traffic, including such vehicles as industrial forklift trucks. The preferred method of protection is to route the piping outside the reach of passing traffic. Where this is not possible, substantial barriers should be erected to protect the piping from impact. Small-diameter piping takeoffs from large headers such as vents, drains, and instrumentation source connections are particularly prone to damage from unspecified external loads. Common design practice is to make the small piping from the header out to the first isolation valve at least one schedule heavier than called for by the pressure design. Similarly, the first isolation or root valve is normally made one or two pressure classes heavier than called for by pressure design considerations. These steps may make the small lines durable enough to resist random impact or other undefined external loadings that can occur during shipping, construction,or operation.
Erosion-Corrosion (Flow-Assisted Corrosion)
When iron or steel corrodes in water, a soluble oxide layer called magnetite is formed. During steady-state conditions, the magnetite attains a constant protective thickness which promotes a uniform corrosion rate. If the magnetite layer is ‘‘swept’’ by a water film deposited by wet steam or by a locally high-velocity jet in a liquid stream, the dissolution rate of the magnetite increases. This results in an increase in the localized corrosion rate and an attendant loss of metal from the surface. Since the sweeping away of the oxide layer is an essential part of this corrosion process, it has been named erosion-corrosion [also known as flow-assisted corrosion (FAC)].
A number of factors have been found to affect the rate of erosion-corrosion (FAC) in piping systems. In wet-steam systems, percentage of moisture, material composition, pH and water chemistry, temperature, oxygen level, and flow path geometry have all been found to be significant. In water piping systems, piping material, temperature, pH and oxygen level, and flow path geometry all affect the rate of erosion-corrosion. Among the variables cited above, two that can be readily controlled in design are the piping system materials and the flow path geometry.
Carbon steel is known to be highly susceptible to erosion-corrosion (FAC). Both chromium-molybdenum (Cr-Mo) and austenitic stainless steels are significantly less susceptible. The EPRI publication ‘‘Erosion/Corrosion in Nuclear Power Plant Steam Piping: Causes and Inspection Program Guidelines’’ cites a study that indicates the rate of erosion-corrosion (FAC) in Cr-Mo wet-steam piping is one-tenth that of carbon steel. Low-alloy Cr-Mo materials can usually be substituted for carbon steel without any other significant design changes. The materials are readily welded to each other, and both have similar physical properties such as tensile and yield strength, density, and thermal expansion coefficient.
The substitution of austenitic stainless steels will normally require some additional engineering. These materials have a thermal expansion rate that averages 50 percent greater than that of plain-carbon steel. Accordingly, increases in terminal reactions and predicted pipe support movements can be expected. These may require that the pipe be rerouted or that different pipe support components be provided.
Piping system geometry plays an important role in mitigating the effects of erosion-corrosion (FAC). High, localized velocities, vortex flow, jet, and direct stream impingement all increase the rate of magnetite dissolution and therefore increase the rate of erosion-corrosion. Gradual transitions in flow section pipe size and geometric changes to smooth out variations in flow velocity and the provision of shallow-angle intersections will all have a beneficial effect. The removal of discontinuities such as weld backing rings and sharp edges at branch connections will also reduce erosion-corrosion (FAC). The areas immediately downstream of valves and flow measurement orifices are frequently prone to erosion-corrosion due to vortex formation. These areas will benefit from the addition of flow liners or the substitution of erosion-corrosion-resistant alloys.