Piping Stress Analysis Services across Calgary Alberta Canada
- Meena Rezkallah, P.Eng.
- Jun 12, 2020
- 6 min read
Updated: Jan 25, 2021
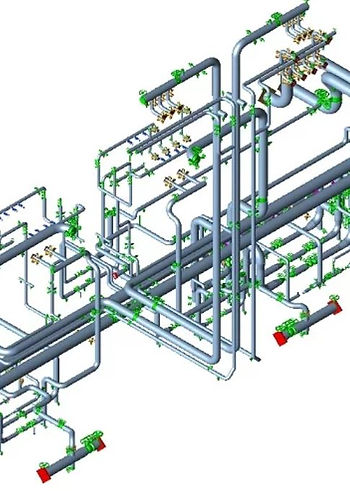
Piping Stress Analysis Services is an analytical system to ascertain the way the piping system acts based on its own substance, temperature, pressure, fluid, and support. Pipe stress analysis isn't a true depiction of this piping behavior, but it's a fantastic approximation.
The analytical approach can function as a review, easy to complicated hand calculations, or even a computer version. The computer models may differ from 1-D beam components to complicated, finite element models. As an example, if it's a water system without the external forces applied to the piping system, review or hands calculations are often adequate. When it's a high pressure, high-temperature, hazardous-fluids system, or large external forces are put on the piping system, a computer-aided model could be deemed necessary.
Recognizing pipe stress analysis applications doesn't make for a good basis for pipe stress analysis. It is important to comprehend the many different kinds of pipe pressures, the procedure, and other things associated with pipe stress analysis Services for the best practices in executing a pipe stress analysis services.
There are numerous piping codes and criteria that might be used over the course of a pipe stress analysis Services based upon the program (power, procedure chemical, gas supply ) and location (province or local authority in Canada); This is why our piping stress engineers are registered professional engineers in Alberta, Saskatchewan, British Columbia and Ontario.
Pipe Stress Analysis Services (thermal flexibility analysis) will predict stresses in piping and loads on equipment resulting from thermal gradients, thermal transients, weights, pressure, and bolt-up strain. This study is typically required for piping that experiences high temperature fluctuations, or for long pipe runs such as hot piping to coolers or headers. Cases where equipment is sensitive to external loads may also require a Pipe Stress Analysis.
The study methodology becomes more complicated for piping systems in vibratory service. As discussed below, the design must address conflicting requirements between the Pipe Stress Analysis Services (where flexibility is desired) versus the Mechanical Vibration Analysis (which requires stiff supports). Methods are available to manage this conflict and create an optimal piping design.
As a standard engineering practice, it is recommended that following lines to be evaluated for pipe stress analysis:
Lines connected to Pressure vessel: All lines 10" and above.
Lines connected to Rotating equipment: All lines 3" and above.
Lines connected to Air cooler / Heat Exchanger: All lines 4" and above.
Lines connected to flare header: All lines 4" and above.
Contact us for our piping stress analysis services free quote
As a part of Piping stress analysis, we would provide simple solutions and would try to use your existing pipe routing as much as possible. We would use tools like Caesar II, Nozzle Pro to analyze pipe / Nozzle for stress evaluation.
The Need for Piping Stress Analysis Services
Pipe Pressure analysis ought to be accomplished primarily to give security to the general public, whether you're designing a building heating system or a high-pressure gas line at a refinery. Public security is paramount.
When a pipe collapse, is a just broken service the owner doesn't connect the designer/engineer about it. On a bad day, the proprietor demands the designer/engineer to cover the damage along with the engineer to offer a solution at no cost.
Another rationale that a pipe stress analysis is done would be to boost the life span of piping. Most engineers will not believe a piece of pipe to function as gear, but It's not any different compared to a pump. It is maintained correctly to ensure a suitable life and to protect gear because a pipe isn't anything more than a significant lever arm attached to some delicate piece of gear. If not properly encouraged and Designed, it could have catastrophic results on this equipment.
There are a few common reasons that could warrant a pipe stress analysis, in addition to those above. They comprise:
Elevated temperatures (>250°F)
Sensitive equipment connections
Enormous D/t ratio (>50)
Piping subject to external pressures.
Critical Services
The Key when doing a pipe stress analysis is determining the necessary level of detail.
Goal Of Piping Stress Analysis Services:
Structural Integrity:
Design adequacy for the pressure of the carrying fluid.
Failure against various loading in the life cycle . Limiting stresses below code allowable.
Optimal Design:
Avoiding excessive flexibility and also high loads on supporting structures. Aim towards an optimal design for both piping and structure.
Governing Codes and Standards:
Codes and Standards specify minimum requirements for safe design and construction (i. e. provides material, design, fabrication, installation and inspection requirements.)
How to Model the Piping System
Pipe Pressure analysis computer versions are a collection of 3-D beam components that produce a depiction of their piping geometry. Three-dimensional beam components are the most effective means to model the piping system, but not always the most precise; and with no complicated finite element models, it's almost impossible to account for all. But, it's known from historic empirical testing these approaches and 3-D beam pc versions reveal enough behavior that they are a fantastic approximation. Additionally, piping codes, for example, ASME B31, have security margins that allow for approximation.
The computer models are just as good as the data entered into them. It's important when creating a pipe stress analysis, just like any finite element analysis (FEA) model, to also know the physics and boundary conditions of the design.
Elements used to model the piping system have their own limits. Thus, ASME has developed stress-intensification factors (SIFs) for piping fittings throughout empirical testing. They allow for increased approximation without using complicated FEA models with bubbles, shells, and brick components. It is vital to be certain these constraints are considered when creating a pipe stress analysis. Most pipe pressure analyses don't function as a high profile FEA software bundle.
Three-Dimensional Beam Component
The 3-D beam component behaviors are ruled by bending minutes. As mentioned above, it's effective for many investigations and adequate for system investigation. But, there are drawbacks to using a 3-D beam component:
No adverse consequences will be viewed on the pipe
No second-order consequences
No huge turning
No accounting for a large shear load
Wall deflection happens before bending failure
Brief, fat cantilever versus extended and skinny
No shell/wall outcomes could be viewed
Working Of Piping Stress Analysis Services:
Pipes would be the most delicate element in almost any process plant, they're also the busiest entities. Piping Systems are exposed to just about all sorts of heaps, intentional or unintentional. It is extremely important to be aware of potential loads a piping system could experience during operation in addition to during other phases in the life span of a process plant. The machine could fail in the first event of the overlooked load. Failure of a piping system can trigger a Domino impact and lead to a significant disaster.
Since the pipe temperature varies from the setup requirement into the functioning state, it expands or contracts. From the overall term, both instances are known as thermal growth. When a tube expands it's the potential of producing tremendous force and pressure within the system. But, if the piping is elastic enough, the growth could be consumed without producing undue pressure or stress.
Piping is used to carry a specific quantity of fluid from one stage to another. It's clear that the shorter the pipe is utilized the lower the capital expenditure is necessary. Long pipe runs can also create excessive pressure fall making it unsuitable for the right operation. On the other hand, the direct shortest design generally isn't suitable for consuming thermal growth. Flexibility evaluation is completed on the piping system to examine its behavior when its temperature varies from ambient to functioning, in order to arrive in the most economical design with sufficient security. Piping flexibility is offered in a number of various ways.
When a pipe is bent inside its elastic limit (no permanent deformation), then it is going to act as a spring and return to its initial shape after the load is removed. When the pliers and elbows to a tube system are organized to permit motion, the forces will be a lot less than a straight run. Additionally, the turns and offsets necessary for running the pipe from one stage to another to provide some versatility too. This inherent flexibility may or might not be sufficient based on individual scenarios.
Little P.Eng. for Engineering Services proudly presents its Licensed Professional Canadian Piping Stress Engineers; Located in Calgary Alberta, we serve our clients across Canada. Our professional piping stress engineers have a bachelor's degree in mechanical / structural engineering and province license (P.Eng.) in Alberta, Saskatchewan, British Columbia and Ontario. We review, validate, certify and stamp piping and structural packages.
Contact US:
littlepenginfo@gmail.com
+1 (587) 802-4050