3.5.3 Evaluation of Restraint Stiffness
- Meena Rezkallah, P.Eng.
- Sep 15, 2020
- 4 min read
Updated: Dec 20, 2020
In Section 2.3.3 of these seminar notes the significant effect that restraint stiffnesses may have on the piping system was described. Assuming restraints are rigid (when they are far from rigid) can lead to grossly conservative designs, possibly resulting in the unnecessary modification of the system. However, assuming that restraints are rigid cannot always be counted on to produce conservative solutions in a complex piping system, either. It is therefore often necessary to refine pipe stress analyses through the use of estimated restraint stiffness. Section 3.4.3 provided one means of doing this, using techniques for estimating an accurate stiffness for piping to vessel anchors.
If the stiffness is not entered by the user, CAESAR II defaults restraints to rigid — i.e., to have a stiffness (translational or rotational) of 1.0E12 lb/in or in-lb/deg. In many cases, this is an extreme overestimate. For example, the stiffness of the "typical" restraint shown in Figure 3-106, can be conservatively estimated to be the stiffness of the bending of the W4X13 wide flange and the extension of the 1-inch diameter rod under load.
The stiffness of the support is calculated as the inverse of the displacement of the support under a one pound load at the pipe, or (for this particular case):

This stiffness is far from 1E12. However the impact of modeling a restraint such as this as rigid depends on the characteristics of the piping system, since the true goal is to simulate a reasonable estimate of the relative stiffness of restraints to pipe. It is best to be concerned about modeling stiffnesses at restraints which obviously do not appear to be "rigid" relative to the pipe. Examples of anchors that should probably be modeled with a less than rigid stiffness are shown in Figures 3-107 and 3-108.
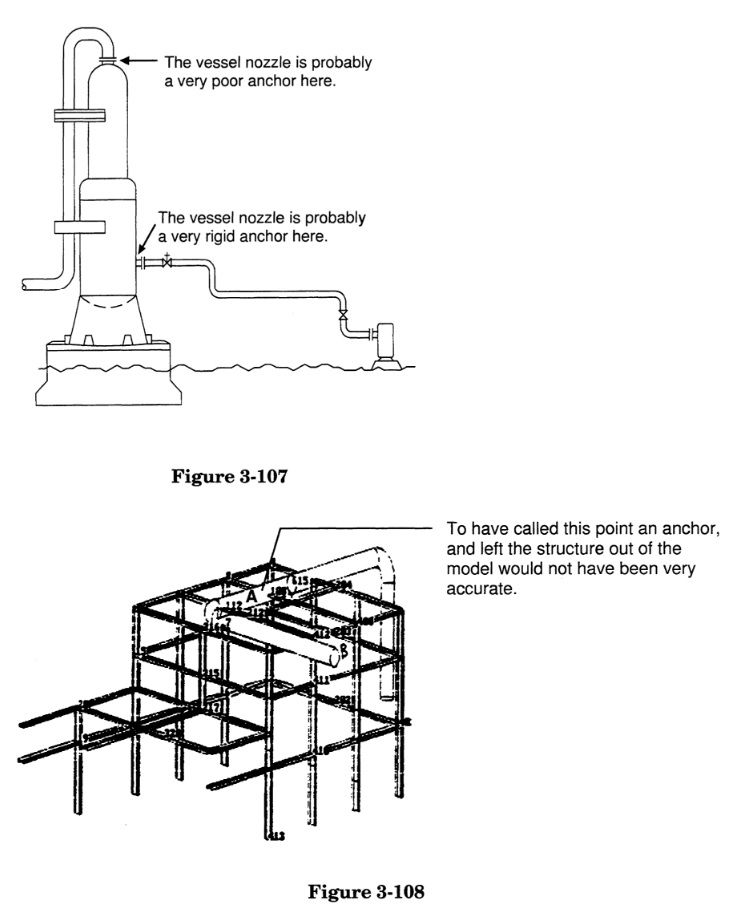
The basic question that should be posed when reviewing restraints for possible modeling of the stiffness is "What is the relative stiffness of the restraint compared to the pipe and the loads being applied?" Influential factors include:
Large, hot, thick walled pipe usually has high axial stiffness and large loads, implying that impacted restraints may be less than rigid in comparison.
Alternatively, for small bore pipe, a restraint of virtually any stiffness probably appears to be rigid in comparison — when analyzing a 2-inch diameter line, results may not change noticeably even if the restraint stiffnesses are entered as 10,000 lb/in or 1E12 lb/in.
Restraints in structures or buildings located high above grade may be affected by the flexibility of the building frame.
It is often difficult to build structures which can "rigidly" restrain moments. This is due both to the low torsional resistance of open sections, and due to the fact that structural members cannot be loaded in the strong axis for all three rotational directions. Performing the analysis using more realistic, flexible moment restraints will most likely cause the restraint to rotate slightly, transferring the moment load elsewhere in the system, and potentially dissipating it.
Connections at the top of tall towers may be flexible due to the lateral flexibility of the structure.
Soil anchors are cumulatively stiff, but locally very weak. It is common to continue buried pipe models for several hundred feet after the pipe has become buried. It is only after this distance that a "cumulative" (virtual) anchor is considered to have been formed. Water hammer loads at buried elbows can cause pipes to "kick out" of the ground. In this case the local soil strength is small, and the local load is very high. (Where this is considered a problem, concrete blocks and supports are poured around elbows that are part of long elbow-elbow pairs.)
It is unrealistic to selectively model in restraint stiffnesses. For example, given three identical restraints in a row, if the center one has its true stiffness modeled and the other two do not, the analysis will force load away from the restraint at the center and toward those on the ends (which will not be the case in reality). It must be remembered when trying for accurate relative stiffness that the stiffnesses must be accurate not only relative to the pipe, but also relative to other supports.
In general, it is safe to say that the results of most analyses will increase in accuracy as the modeled restraint stiffnesses increase in accuracy.
Restraint stiffness can be calculated manually, as was done for the restraint shown in Figure 3-106 and simply entered into CAESAR II when coding in the restraint. An alternative is to construct a partial model of the restraint as part of the piping system, using either pipe elements or structural members. For example, the flexibility of tall vessels can be modeled with pipe elements down to the foundation. In the case of structural steel models, often including only a small part of the model is sufficient to improve the behavior of the restraint. Complex structural steel models may be incorporated in to the piping system using the structural steel modeler, accessible from CAESAR II's main menu.
Read More:
Located in Calgary Alberta, We offer our Piping Stress Analysis Services and Structural Engineering Services across Canada.
Our structural Engineers / piping stress engineers have a bachelor's and Master's degree in mechanical / structural engineering and province license (P.Eng.) in Alberta, Saskatchewan, British Columbia and Ontario. We review, validate, certify and stamp piping and structural packages.
#piping_engineering_services #piping_engineering_consultant #piping_skid_design #piping_stress_analysis #piping_engineering_firm #piping_engineering_company #asme #engineeringservices #engineering #engineers #engineer #engineering_services #engineering_firm #engineering_company #engineering_consultant #pipe_stress_analysis #pipes #calgary #meena_rezkallah #pipe_stress_engineer #piping_stress_engineer #pipe_stress_analysis_services #edmonton #pipe_stress_analysis_company #ontario #pipe_stress_analysis_firm #piping_standards #CAESAR_II #pipingengineer #pipingstressengineer #BC #Vancouver #British_Columbia #toronto #fortmcmurray #saskatchewan #skid_design #jobs #engineering_consultant #Engineering_Company #Piping_Engineering_Company #Structural_Engineering_Company #Engineering_Firm #Piping_Engineering_Firm #Structural_Engineering_Firm #Canada #Alberta #Ontario #Saskatchewan #British_Columbia #Piping_Engineer #Piping_Stress_Engineer #Structural_Engineer #Meena_Rezkallah #Pipe_Stress_Analysis_Company #Pipe_Stress_Analysis_Firm #Pipeline_Engineering_Company #Pipeline_Engineering_Firm #Saudi_Arabia #United_Arab_Emirates #Oman #Qatar #Kuwait #Dubai #ABU_DHABI #Texas #Houston